A combination of factors, most of which have derived from the continuing global pandemic, have culminated in the severe semiconductor shortages, posing significant challenges for car manufacturers worldwide.
Semiconductors themselves, in modern society, are indispensable in the manufacturing of essentially all electronic devices that we in the developed world have come to take for granted. Ranging from mobile phones and computers to washing machines and other domestic appliances, and even the infotainment and safety systems integrated into modern vehicles, these tiny integrated circuits measuring just billionths of a meter play a crucial role in our daily lives.
Without semiconductors, our world would be fundamentally different in almost every conceivable way as entertainment, transport, commerce, and domestic life all depend on these essential components.
The Covid-19 pandemic caused a rapid decline in industrial production, resulting in shortages of sundry goods and products in the global market. Thousands of factories responsible for manufacturing semiconductor chips were closed down indefinitely due to the virus, leading to a scarcity of supply. This shortage, in turn, impacted various industries in different ways.
Demand for mobile phones, laptops, gaming consoles (especially with the release of the next-generation platforms), and other electronic devices soared as many people confined to their homes experienced a craving for entertainment that these appliances gladly satiated or were forced to work online. As a result, the computing and electronics industries witnessed a surge in demand for semiconductor chips, leading semiconductor manufacturers to grant them priority over those in the motoring industry.
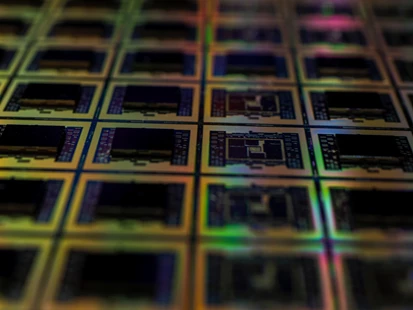
Although a vast quantity of modern vehicles incorporate semiconductor chips to power their sophisticated infotainment and safety systems, the motoring industry and automotive companies account for only a relatively small percentage of semiconductor manufacturers’ revenue compared to electronics and IT firms.
As a result of the semiconductor shortages and the considerable increase in the sales of electronic devices, semiconductor manufacturers have given precedence to companies within the computing and electronics industries, affecting the production capabilities of car manufacturers.
Initially, vehicle manufacturing groups, such as General Motors and Volkswagen Group, closed down production lines and canceled all orders for semiconductor chips in response to the pandemic and the seemingly inevitable global market stagnation that would continue for a protracted period of time.
However, in the third quarter of 2020, vehicle sales recovered at an unanticipated rate, causing demand for semiconductors to rise quickly within the motoring industry. This rapid shift caught many car manufacturers off guard, and they struggled to keep up with the sudden surge in demand for semiconductor chips.
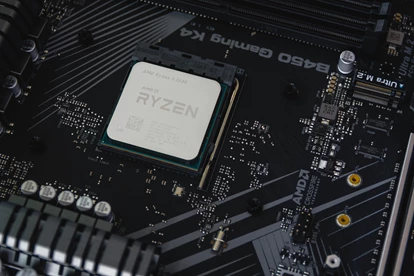
The impact of the semiconductor shortage on vehicle manufacturing has been profound, with significant disruptions in the production process. In the UK, for example, only approximately 55,000 cars were assembled in May 2021, according to the Society of Motor Manufacturers and Traders. This number is less than half of the 116,035 vehicles produced in the same month in 2019, before the outbreak of the pandemic.
The dearth of chips also caused both Jaguar Land Rover and MINI to temporarily cease production at their assembly lines in the UK. Additionally, Ford estimated that they would produce 1.1 million fewer cars this year. Some manufacturers have thus adopted a more reserved mindset, with certain vehicles being stripped of certain features, or having digital displays substituted with analogue ones to cope with the chip scarcity.
Unfortunately, this scarcity is expected to continue into 2022, with further effects on car manufacturing yet to be seen. The supply chain pressures inflicted by national lockdowns and restrictions, as well as the US-China tech war that has arisen due to geopolitical tensions and ambitions to dominate chip manufacturing, have made it challenging for integrated circuit (IC) manufacturers to satisfy the substantial demand from both car manufacturers and electronics firms.
The semiconductor shortages have taught car manufacturers the importance of diversifying supply chains and reducing reliance on a limited number of chip suppliers. Many are now working on establishing strategic partnerships and investing in local production capabilities to mitigate future disruptions.
The impact of these shortages on the automotive industry serves as a crucial reminder of the interconnectedness of the global supply chain and the need for contingency planning in the face of unforeseen events.
In conclusion, the ongoing semiconductor shortages have had severe consequences for car manufacturers worldwide. The sudden shift in demand for semiconductors caught the industry off guard, leading to disruptions in vehicle production and a decline in car assembly. To address future challenges, car manufacturers must prioritize diversification and strategic planning to ensure resilience in the face of unpredictable events. Only then can the industry navigate through the rough waters of semiconductor shortages and emerge stronger in the ever-evolving world of technology and manufacturing.
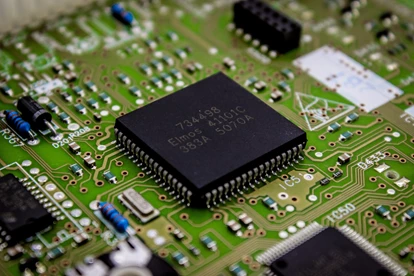